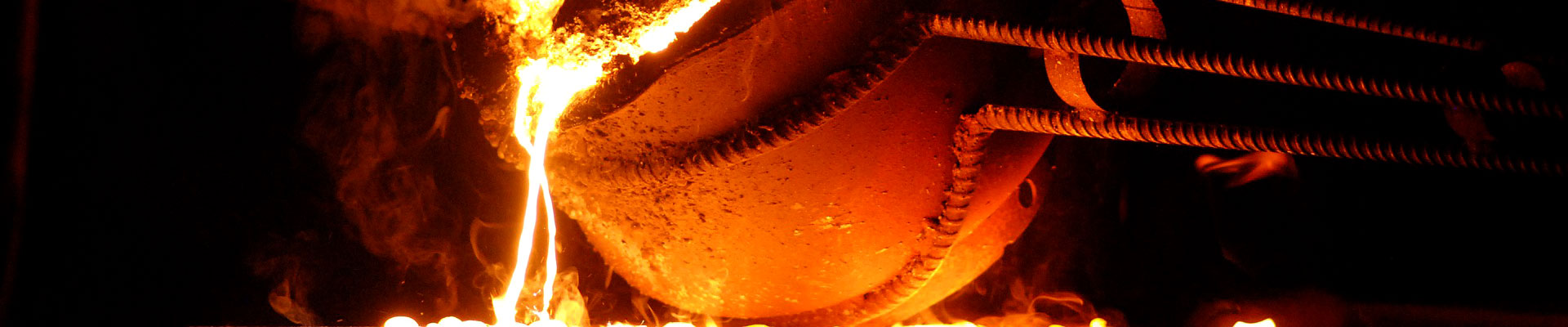
Casting Processes
According to the American Foundry Society, a casting is a metal part formed by pouring molten metal into a sand mold or metal die during the casting processes. After the metal solidifies, the mold is broken, the cores removed, and the part is prepared for machining and finishing operations.
Commonly used processes in metal casting facilities include:
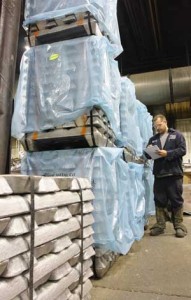
Advanced Quality Management
CFI partners with high-quality metal casting operations that understand the importance of producing cast products meeting your need for quality and workmanship. Our ISO-certified partners use the latest quality techniques and computer programs to assure your project conforms to all quality requirements at every step of the production process.
What Metals Should You Select?
Virtually any metal that can be melted can be cast in foundries today. We’ve listed the most common metals used in metal casting for your convenience. Keep in mind that we will assist you in selecting the specific alloy necessary for your project.
For example, you may know that you need an aluminum die cast component for its strength and light weight; however, you may not know which aluminum alloy will give you the best results for your specific application. Choosing the wrong alloy can result in part failure, shorter part life and parts not performing up to expectations.
Ferrous Metals | Nonferrous Metals |
---|---|
Gray Iron | Brass |
Ductile Iron | Bronze |
Malleable Iron | Nickel-Base Alloys |
Meehanite Iron | Zinc-Base Alloys |
Steel | Aluminum Alloys |
Carbon and Low Alloy Steel | Sand Cast Permanent Mold Alloys |
Corrosion-Resistant Stainless Steel | Die-Cast Alloys |
Heat Resistant Stainless Steel | Aluminum-Magnesium Alloys |
Manganese Wear Resistant Steel | Magnesium Alloys |
Definition of Terms
CASTING
Metal object cast to the required shape by pouring or otherwise injecting liquid metal into a mold, as distinct from one shape by a mechanical process. Act of pouring molten metal into a mold during the casting processes.
PATTERN
A form of wood, metal or other materials, around which molding material is placed to make a mold for casing metals.
CARBON STEEL CASTINGS
Steel that owes its properties chiefly to the presence of carbon, without substantial amounts of alloying elements (ordinary steel, straight carbon steel, plain carbon steel).
STAINLESS STEEL CASTINGS
A wide range of steels containing chromium and nickel, exhibiting high resistance to corrosion.
TOOL STEEL
Any high-carbon or alloy steel used to make a cutting tool for machining metals and for metal casting dies.
MANGANESE CASTINGS (HATFIELD STEEL)
A work hardening cast steel containing 12 to 14% manganese.
IRON CASTINGS
Essentially an alloy of iron, carbon (2-4%) and silicon in which the carbon is present in excess of the amount which can be retained in solid solution in austenite at the eutectic temperature. When cast iron contains a specially added element or elements in amounts sufficient to produce a measurable modification of the physical properties of the section under consideration, it is called alloy cast iron. Silicon, manganese, sulfur, and phosphorus, as normally obtained from raw materials, are not considered alloy addition.
NI-HARD
Hard white cast iron containing 4% Ni and 2% Cr.
MEEHANITE CASTINGS
Meehanite Metal castings cover any casting within the overall cast iron composition range that have been produced by the Meehanite process.
This process involves a number of patented procedures seeking to control and produce the desired graphite distribution and the desired matrix structure in the casting. It depends primarily on the establishment of a melt of desired degree of undercooling often referred to as constitution and the controlled nucleation of this melt, usually by means of alkaline earth silicide additions. It requires very careful selection of raw materials, meticulous process controls and a very thorough knowledge of the foundry behavior of cast iron.
The Meehanite process involves the use of standard procedures in all phases of casting manufacture including gating and risering techniques, sand control testing methods and many specialized molding procedures. It seeks to eliminate guesswork, thereby resulting in an engineering product of high integrity and reliability.
MEEHANITE METAL TYPES
While the Meehanite process is a closely integrated procedure and will produce a truly quality casting, it’s necessary for the engineer to have at his disposal exact figures on the physical and mechanical properties of Meehanite Metal so that he may design with confidence. For this reason, Meehanite Metal has conveniently been divided into a number of broad type classifications each with its typical properties, which enables the engineer to select that type of metal most, suited to his particular application.
On the basis of use, the following broad categories apply:
General Engineering | Prefix G |
Wear Resisting | Prefix W |
Heat Resisting | Prefix H |
Corrosion Resisting | Prefix C |
These categories relate to the end use of the casting and are further sub-divided on the basis of metallurgical structure and property values.
ALUMINUM CASTINGS
Aluminum is the most abundant metal in nature, a metallic element of 2.7 atomic weight 26.97, atomic number 13, mp 1220 F (660 C). Extensively used for castings, foundry patterns and core driers and as a deoxidizer in iron and steel making.
BRASS CASTINGS
Copper base alloys with zinc as the major alloying element.
BRONZE CASTINGS
Copper-base alloys, with tin as the major alloying element; further defined in relation to second major alloy element, as silicon bronze, aluminum bronze.
ZINC CASTINGS
Predominant alloying element in brass, a metallic element with mp of 419 C (786.2F); used extensively in die castings and as a corrosion-resistant coating for ferrous alloys.
SAND CASTINGS
Metal castings produced in sand molds
DIE CAST FOUNDRY
A rapid, water cooled permanent mold casting process, an outgrowth of casting printer’s lead, still quite limited to nonferrous metals. There are three types: the plunger type operated hydraulically, mechanically or by compressed air with or without a gooseneck; the direct-air injection which forces metal from a gooseneck into the die, and the cold-chamber machine. All force the metal into the die with a pressure greater than that of gravity flow.
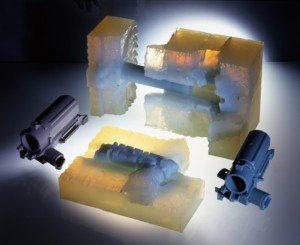
Investment and Lost Wax Casting
INVESTMENT CAST FOUNDRY
The process of casting metal into an investment mold. See also lost wax process.
LOST WAX PROCESS
A casting process in which a wax or thermoplastic pattern is used. The pattern is invested in refractory slurry; after the mold is dry; the pattern is melted or burned out of the mold cavity. Also, investment casting, precision casing.
PRECISION CASTINGS
(See Lost Wax or Investment Cast)
PERMANENT MOLD
A two or three-part mold of metal or graphite which can be used repeatedly for the production of many castings of the same form. Liquid metal is poured in by gravity.
NOBAKE FOUNDRY
Where you use a binder-a synthetic liquid resin sand binder that hardens completely at room temperature, generally not requiring baking, used in cold-setting process.