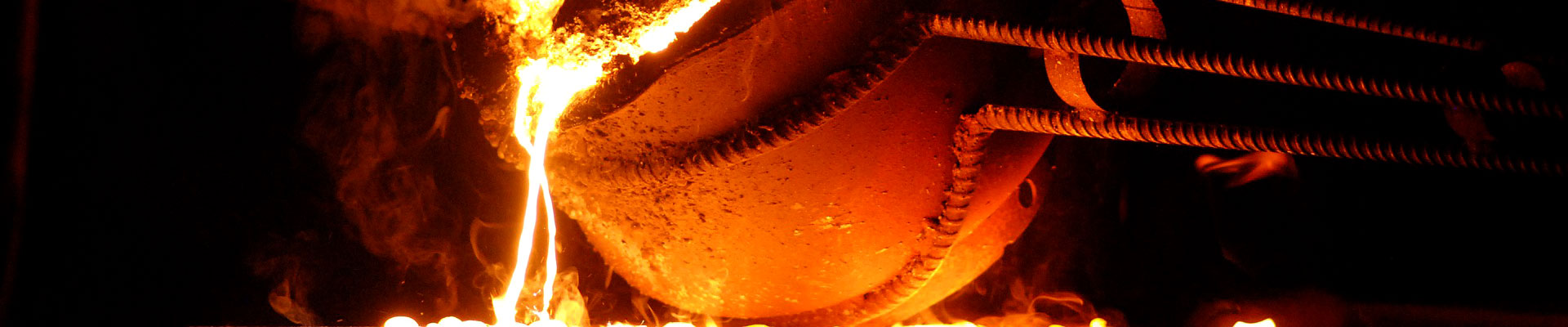
Shell Molding
Probably the earliest most automated and most rapid of mold and core making processes was the heat-curing technique known as the Shell Molding process. Resin-bounded silica sand is placed onto a heated pattern for a predetermined time. Ejector pins enable the mold to be released from the pattern and the entire cycle is completed in seconds depending upon the shell thickness desired. The two halves of the mold, suitably cored, are glued and clamped together prior to the pouring of the metal. Shell molds may be stored for long periods if desired. Because of pattern cost this method is best suited to volume production. Designers should seek the advice of the foundry to ensure that all the benefits of the process are achieved.
Advantages
Shell Molding molds may be stored for extended periods of time. Good casting detail and dimensional accuracy. Mold is light in weight.
Disadvantages
High pattern cost, high pattern wear (sometimes), high energy cost, higher material cost compared to green sand molding.
Chemically Bonded Molding
Shell Molding
Typical dimensional tolerances, inches | ± .005″, ± .015″ |
Relative cost in quantity | Medium High |
Relative cost for small number | Medium High |
Permissible weight of casting | Ounces to 250 lbs. |
Thinnest section castable, inches | 1/10″ |
Relative surface finish | Good |
Relative ease of casting complex design | Good |
Relative ease of changing design in production | Fair |
Range of alloys that can be cast | Unlimited |
Parting Line Influence
When Parting lines are considered, very close tolerances are difficult to obtain. A parting line absorbs fractions of inches per inch. A foundry is doing well to hold a parting line to 0.015 inch. Additional measurement is added to the casting tolerance.