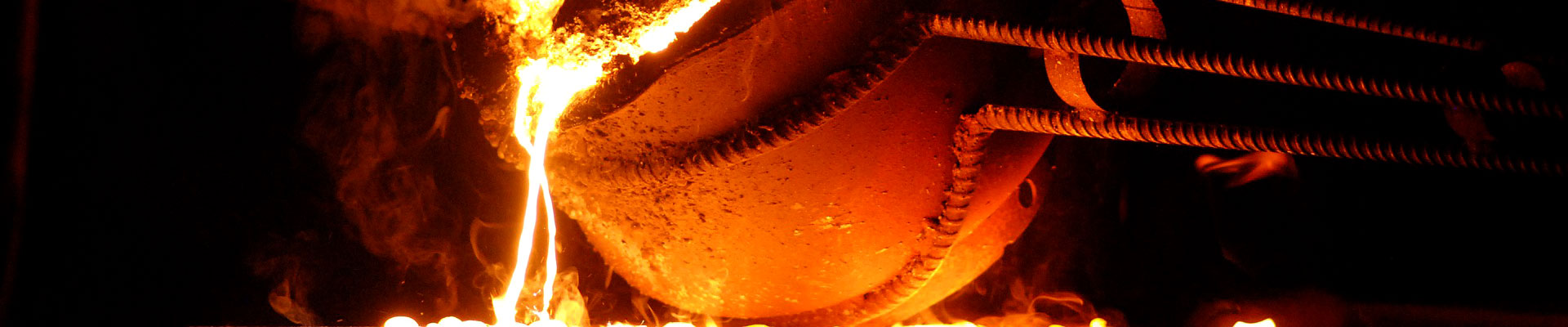
Gray Iron Castings
Gray iron is the most versatile of all foundry metals. The high carbon content is responsible for ease of melting and casting in the foundry and for ease of machining in subsequent manufacturing. The low degree or absence of shrinkage and high fluidity provide maximum freedom of design for the engineer.
The general composition of gray cast iron is 95% iron by weight with an additional 2.1 to 4% being carbon and 1 to 3% silicon. Manganese and other impurities are also commonly found in or added to molten iron as needed for the diminishing or enhancement of specific properties. Sulfur, for example, is commonly introduced to the molten metal in order to increase hardness, which is otherwise low in most cast iron components.
Gray iron casting has a high amount of silicone, which is responsible for the production of graphite when the alloyed materials are heated. The deflection of this graphitic microstructure gives the metal its gray appearance. By comparison, ductile cast iron production slows down the growth of graphite and allows the carbon to separate as spheroidal graphite particles instead.
Through suitable adjustment in composition and selection of casting method, tensile strength of gray iron castings can be varied from less than 20,000 psi to over 60,000 psi and hardness from 100 to 300 BHN in the as-cast condition. With subsequent heat treatment, the hardness can be further increased. However, component requirements should be carefully reviewed before specifying a higher strength and hardness grade of iron. An unnecessary increase in strength and hardness may increase the cost of the casting as well as increase the cost of machining through lower machining rates.
The casting process can have a significant effect on the structure and properties of gray iron casting. The processes using sand as the mold media have a somewhat similar effect on the rate of solidification of the casting, while the permanent mold process has a very marked effect on structure and properties.
Green sand molding is frequently the most economical method of producing castings. Although castings up to 1,000 pounds or more can be made in green sand, it generally is used for medium to small size castings. If green sand molds are not sufficiently hard or strong, some mold wall movement may take place during solidification, and shrinkage defects develop. For the larger castings, the mold surfaces are sometimes sprayed with a blacking mix and skin dried to produce a cleaner surface on the casting. This procedure is often used on engine blocks.
To withstand the higher ferrostatic pressures developed in pouring larger castings; dry sand molds are often used. In some cases, the same sand as used for green sand molding is employed, although it is common practice to add another binder to increase the dry strength.
The shell molding process is also used for making cores, which are used in other types of molds besides shell molds. The primary advantage is the ability to harden the mold or core in contact with a heated metal pattern, improving the accuracy and finish of the casting.
Centrifugal casting of gray iron in water-cooled metal molds is widely used by the cast iron pipe industry as well as for some other applications. With sand or other refractory lining of the metal molds, the process is used for making large cylinder liners.
Gray iron casting is used in many market segments, including automotive, agricultural, machinery building, electronics, irrigation, ventilation, architecture, construction and transportation industries.