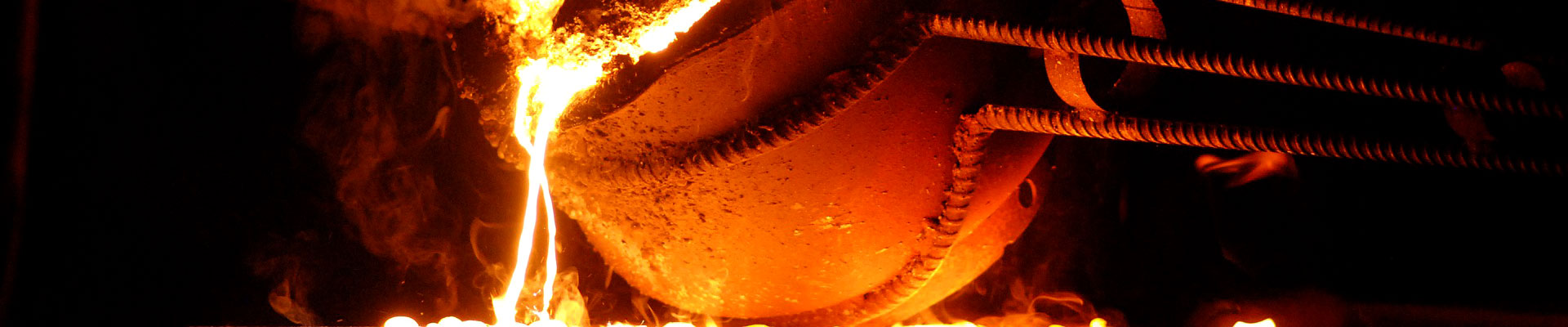
Casting Metals & Alloys
Casting Metals and Alloys are divided into groups based on composition.
Ferrous Metals
Ferrous Metals may be subdivided according to carbon content and classified as steel or cast iron.
Nonferrous Alloys
Nonferrous Alloys are classified according to the base elements of which they are composed. The base elements commercially are mainly copper, aluminum, magnesium, lead, tin, and zinc. To obtain the desired physical and mechanical properties, it is necessary to vary the amounts of these elements.
Alloy
An alloy is a substance having metallic properties and composed of two or more chemical elements of which at least one is metal. You get different specific types of metal by combining the base alloy with other alloys to bring steel, iron, aluminum, brass, bronze or any other grade of material to a specific grade much like a receipt in your own kitchen. Each application may call for something different such as hardness, tensile strength, wearability or resistance to corrosion etc.
Then each casting may have to be annealed heat treated quenched and tempered or a combination of several of these processes.
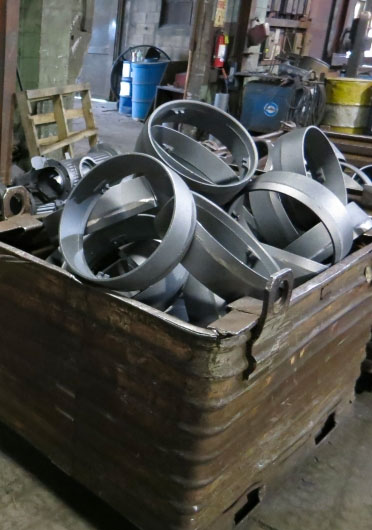
Ferrous Metals – Casting Metals and Alloys
Typical casting groups classified as ferrous grades of metal are as follows:
Gray iron castings can be cast in various tensile strength ranges from soft, machineable, low strength irons of near 20,000 psi tensile strength to hard, wear-resistant irons of 60,000 psi.
Various casting markets are served by individual classifications of gray iron, noted as follows:
Class 20 | Class 30 | Class 40 | Class 50 |
---|---|---|---|
Ingot Mold | Auto | Valves | Engine |
Municipal | Farm | Machine Tool | Special Industries |
Soil Pipe | Construction | Machinery | Compressor |
Motors | Home Appliances | Gears | Pumps |
Class 60 | White Iron Ni-Hard High Chrome | Alloyed Irons, Ni-Resist | Compacted Graphite Iron |
---|---|---|---|
Engine | Metalworking Engine | Engine | Molds and Stools |
Machine Tool | Cement | Pumps | Exhaust Manifolds |
Mining | Rolls | Food Production | Flywheels |
Gears | Coal Pulverizer | Marine | Axle Housings |
Hydraulic Valves |
Since ductile iron was developed in the 1940s, this remarkable metal has proved its value in tens of thousands of engineering and casting applications. Ductile iron is created by an alloying process which converts the crack-promoting graphite flakes of gray iron into nodules. With this microstructural transformation, the metal acquires superior ductility, elongation characteristics, and machinability. The ductile iron family offers the design engineer a unique combination of strength, wear resistance, fatigue resistance, and toughness, as well as excellent ductility characteristics.
Ductile iron combines the processing advantages of gray iron (low melting point, good fluidity and castability, and ready machinability) with many of the engineering advantages of steel (high strength, ductility and wear resistance), which allows for higher material properties as tensile and yield strength than gray iron. Table 4 shows the properties for various grades of ductile iron.
In all its grades, ductile iron exhibits mechanical properties that make it an ideal alloy for sand and investment castings.
Various market segments and casting types are served by the following grades:
60-45-15 | 80-55-06 | 100-70-03 |
60-45-12 | 80-60-03 | 120-90-02 |
60-40-18 | 130-100-04 |
Various casting markets are:
Valves | Pumps | Refrigeration |
Pipe | Electric | Gears |
Farm | Motor Vehicles | Tool and Dies |
Construction | Machine and Tool | Shafts |
Special Industries | Machine Tool | Farm Equipment |
Malleable Iron is a desirable engineering material because of its ease of machineability, its toughness, ductility, and wide range of strengths. Some of the principal industries using castings made of malleable iron are: automotive, hand Tools, valves and fittings. Malleable iron castings continue to decline in usage due to the competitive advantages of ductile iron.
Meehanite Metals are a licensed process for the manufacture of gray flake and nodular cast irons. In the early period of American metal casting, 1900-1930, the metallurgical theories of irons were not well understood. Certain foundry practices were known to produce consistent metals. These irons were typically called Pro-Iron or Semi-Steel. Meehanite developed set procedures which produce a high quality engineered iron which permitted engineers and designers to rely upon the integrity of the metal. Meehanite at the time corresponded to Semi-Steels. The meehanite process filled a void until metallurgy, the science caught up with the art form of the metal casting trade. With the advent of specifying and testing bodies such as A.S.T.M., S.A.E., and military specifications, uniform physical, mechanical, and chemical properties were required of the metal casters. Uniformity has caused designers or buyers to designate metal types according to desired end use. A.S.T.M. and meehanite both specify the same final properties. Therefore, in selecting a meeehanite metal, it can be crossed referenced to any other specifying body with assurance that all will be obtained as specified.
If the Meehanite Metal Handbook is compared to the Iron Casting Society’s Handbook or to the A.S.T.M. Specifications for irons, it is easily seen that there are no differences between Meehanite and other specifying bodies.
Meehanite flake gray irons are designated by letter:
GE – Class 30 | GA – Class 50 |
GD – Class 35 | GM – Class 60 |
GC – Class 40 |
Nodular irons are proceeded by the letter S, Abrasion by the letter W, Heat resisting by the letter H, and Corrosion by the letter C.
Any Meehanite Metal selected can be certified to A.S.T.M. standards.
Steel is an alloy of iron and carbon that may contain either elements and in which the carbon content does not exceed approximately 1.7%.
Steel is considered the ideal metal for many types of casting applications because its chemical analysis as well as its mechanical and physical properties are easily varied over a wider range than other cast metals. This is achieved by varying the carbon content, the chemical composition, or by heat treatment. It is strong, tough, dependable, and readily joined by welding or bolting to other metal forms, such as rolled products, forgings, or other castings. Steel castings are used in many industries. These include railroad, automotive, marine, farm equipment, machinery for highway, construction, mining, metalworking, power transmission, valves and fittings.
Markets for carbon and low alloy steel castings include the following:
Valves | Turbine |
Construction | Mining |
Oil Field | Milling and Metalworking Machinery |
Pumps | Trucks |
A wide range of steels containing chromium or chromium and nickel exhibiting high resistant to corrosion or heat.
The corrosion resistant casting alloys are those compositions consisting basically of nickel, chromium and iron, sometimes including other alloying elements, which perform satisfactorily when used in a large variety of corrosive environments. Castings made of these materials offer two basic advantages: Facility of production of complex shapes at low cost. (The ease of securing rigidity and high strength to weight ratios).
Corrosion-resistant Stainless steel castings used in the following markets:
Ship Propellers | Impellers |
Ship and Boat Building | Internal Combustion Engine Turbines |
Special Industrial Machine Components | Oil Field Machinery and Equipment |
Valves and Fittings | Roll Mill Machinery |
The heat-resistant casting alloys are compositions of performing satisfactorily when used a temperatures above 1200° F. Heat resistant casting alloy combinations are composed principally of nickel, chromium and iron, together with small percentages of other elements. Nickel and chromium both contribute to the superior heat-resistance of these alloys. Castings made of these alloys meet two basic requirements:
- Good surface film stability (oxidation and corrosion-resistance) in various atmospheres and at temperature to which they are subject; and
- The necessary mechanical strength and ductility to meet high temperature service conditions.
Heat-resistant stainless steel markets is as follows:
Nonelectric Heating | Tool and Dies |
Industrial Furnaces and Ovens | Mining |
Blowers and fans | Rolling Mill Machines |
Valves | Oil field equipment |
Power Plants |
Manganese alloy steels, which cannot be made except by the casting process, have excellent resistance to wear: they work-harden during use.
Potential markets include:
- Construction and mining equipment
- Special industrial machinery
- Railroad equipment
- Crushing Equipment Industry
Any high-carbon or alloy steel used to make a cutting tool for machining metals and for metal casting dies.
Nonferrous Metals – Casting Metals and Alloys
Nonferrous alloys are classified according to the base elements of which they are composed. The base elements used commercially are mainly copper, aluminum, magnesium, lead, tin, and zinc. To obtain the desired physical and mechanical properties, it is necessary to vary the amounts of these elements. Typical nonferrous grades of metal most commonly used are as follows:
Copper-based alloys of copper and zinc are commonly classified as brass. Copper-zinc are the major group of metals used, due to their desirable properties and relatively low cost.
Yellow brass is the most ductile of all the brasses. Its ductility makes possible the use of this alloy for jobs requiring the most severe cold-forging operations, such as deep-drawing, stamping, and spinning.
Red brass is composed of 2% to 8% zinc, has a reddish color, a great resistant to corrosion, and good workability. Red brass alloys have good casting and machining characteristics. They are readily shaped by stamping, drawing, forging, and spinning. Applications of red brass include valves, fitting, rivets, radiator cores, plumbing pipe, flexible hose, and cloth.
When tin is added to copper as a secondary alloy element, bronze is produced. Hardness and wear resistance are increased, although, although ductility is decreased. Tin bronzes have excellent resistance to corrosion and good properties at elevated temperatures. When lead is added and excellent bearing bronze is produced which is useful as a bearing material.
Yellow bronze, with more than 17% zinc and more than 2% aluminum, manganese, iron, and tin, is known as manganese bronze. Manganese and iron, which are added to obtain the desired physical properties, can increase tensile strengths from 60,000 to 120,000 psi.
Copper-rich alloys of aluminum and copper are known as aluminum bronze, which has a near-gold color, possesses a good finish, and is highly resistant to acid.
One of the many grades of bronze, which is red in color and contains 1% to 5% silicon, is known as silicon bronze. These casting metals and alloys have good resistance to salt water, alkalies, and acids. Small amount of zinc, tin, and iron may also be present.
Nickel-base alloys have great resistance to corrosion in the presence of most mineral acids, most organic acids, and alkalies. They are not resistant by oxidizing salts. They have good mechanical strength, ductility, and resistance to wear, although they cannot be used for bearings, except under light loads and at slow speeds.
An alloy of 70% nickel and 30% copper is known as Monel. When silicon is added to it, it becomes age-hardened, and thus more wear-resistant. An alloy of 80% nickel and 20% chromium, known as Nichrome, is used for electrical resistance heaters. An alloy of 80% nickel, 14% chromium, and 6% iron, known as Inconel, is used where oxidation resistance with high strength at elevated temperatures is needed.
Casting Metals and Alloys with high percentage of nickel are used for chemical equipment, such as implements used in the dyeing of textiles and the manufacture of caustics, as well as for making water-softening equipment, valves and pumps parts, and food-handling equipment.
An alloy consisting of 20% zinc, 20% manganese, 1% aluminum, and the balance copper produces white-bronze casting that is strong, ductile, and corrosion-resistant. It can be polished to a high, silvery luster which makes it useful in architectural and marine hardware, plumbing fixtures, ornamental castings, hospital equipment, and swimming pool equipment.
Casting markets using brass, bronze copper, and copper-base alloys include the following:
- Plumbing valves and sanitary fixtures and fittings
- Pumps
- Electric Equipment and apparatus
- Power transmission equipment
- Marine hardware and ship propellers
- Metalworking machinery and equipment
- Ball and roller bearings
Zinc base alloys are wide used in die casting. The alloy elements are principally copper, aluminum, and magnesium. The amount of each used depends on the properties desired. High purity zinc is used as the base metal, the addition of copper increases the strength, but reduces ductility. Addition of aluminum improves the strength of the alloy and delays the rate of attack of the alloy on steel dies, and thus improves the life of the die. Additions of magnesium added to the dimensional stability of the die casting.
Casting Metals and Alloys development is a continuous process and the producers should be contacted when there is a question regarding the alloy to be used with the casting process being considered.
Zinc die casting include the following:
- Bathroom and plumbing fixtures
- Door, window and furniture hardware
- Hand tools
Pure aluminum is a poor casting material and is limited to the casting of rotors where high electrical conductivity is an advantage. Almost all aluminum castings are made of an alloy of aluminum. The selection of a particular alloy depends on the criteria demanded of the alloy- the mechanical strength, machinability, surface appearance, resistance to corrosion, conductivity, pressure tightness, and other factors. The principal alloying elements are copper, silicon, magnesium, zinc, chromium, manganese, tin, and titanium. Iron is often present in small quantities, and is usually considered an impurity. Although all of the alloys are commercially castable by a specified process, namely sand casting, permanent mold casting, or die casting, the casting industry has established a preference for certain alloys in each casting process.
In sand casting and permanent mold, alloys with additions of silicon in the range of from 5% to 8% copper in the 1% to 5% range, and magnesium in the 0.2% t0 1% range are used to produce most aluminum castings.
Sand cast and permanent mold aluminum casting markets are as noted:
- Internal combustion engine
- Lawn and garden equipment
- Power hand tools
- Office machines and computers
- Aircraft parts
- Household appliances
In die casting, approximately 80% of the castings produced use an alloy with addition of 2% to 5% copper, 7% to 10% silicon, 1% to 3% zinc, and 1% iron.
Castings produced using the die-casting process are used for the following:
- Automotive and truck combustion engines
- Furniture, fixtures household appliances
- Toy, sporting goods, bicycles, motorcycles
- Motors, generators, regulators, instruments
Aluminum-magnesium alloys are characterized by excellent mechanical properties and machinability, as well as resistance to corrosion. They have good resistance to impact and high ductility.
These casting metals and alloys are used in:
- Marine applications
- Highway fixtures
Magnesium high purity alloys with various amounts of aluminum, zinc, zirconium, and rare earths are used to produce sand castings, permanent mold castings, and die casting, with die casting the predominant method.
Magnesium die casting markets include the following:
- Aircraft components
- Power tools and sporting goods
- Automotive – transmission cases, clutch housing, timing chain covers, wheels, hinges, brackets, brake pedals, head lamp frames, oil filter adapters, etc.