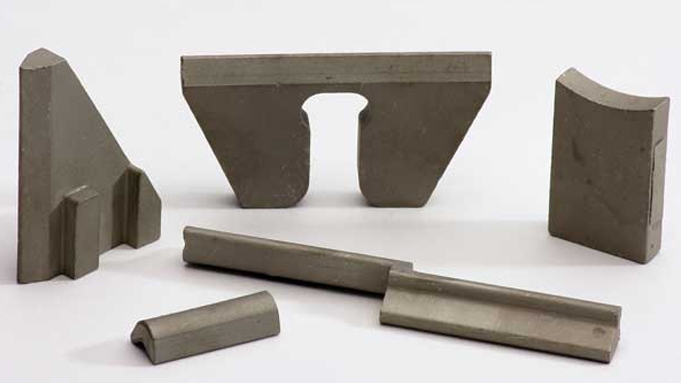
The following table summarizes the advantages and disadvantages of the different casting pattern classes types of pattern equipment used by metal casters.
Pattern Type | Advantages | Disadvantages |
---|---|---|
Wood Loose | Low cost to produce. Use to produce plastic casting pattern classes. Easily modified. | Not suitable for production batches unless converted into plastic before becoming worn. Tend to become inaccurate and to produce poor surface finish. |
Hardwood | Inexpensive for small-batch production. Can be used as masters for plastic patterns. Fairly easily modified but expensive if multiple impressions involved. | Fair wearing properties. With care, will remain reasonably accurate over fairly long periods. Not suitable for high-volume production. |
Plastic | Inexpensive to produce. Urethane technology provides good wearing properties and accuracy. Easily modified depending upon the materials used. Suitable for high-volume production patterns with the same dimensional tolerances as metal patterns. | Urethane technology has reduced many of the disadvantages of early plastic pattern materials. |
Metal | Excellent wearing properties. High standard of accuracy and stability. Suitable for high-volume production and shell molding. CAD/CAM improvements are greatly reducing cost and lead time requirements. | Costly. Difficult to modify. Equipment is less adaptable for movement from one foundry to another. |
Contact Us for any questions about the pattern type for you.
Recent Comments